Metal Stamping: Key Considerations for Quality and Efficiency
Metal Stamping: Key Considerations for Quality and Efficiency
Blog Article
Making The Most Of Effectiveness and Quality With Cutting-Edge Metal Stamping Strategies
In the world of metal marking, the quest of functional quality via the combination of ingenious methods is paramount. As sectors evolve and needs for precision and efficiency rise, staying ahead of the contour comes to be a critical essential. By welcoming advanced modern technologies and procedure improvements, companies can unlock brand-new levels of performance and product high quality. The intersection of sophisticated steel stamping methods, automated systems, rigorous quality assurance, and lean production concepts offers an alluring glimpse right into the future of production. This convergence holds the pledge of not simply meeting however going beyond industry requirements, establishing the phase for unrivaled performance and customer satisfaction.
Advanced Metal Stamping Technologies
In the realm of metal marking, the assimilation of innovative technologies has actually reinvented the sector, boosting accuracy and efficiency in producing processes - Metal Stamping. Advanced metal stamping innovations have played a critical role in raising the capacities of manufacturers, enabling even more intricate designs and higher manufacturing rates
Among one of the most substantial advancements in metal marking modern technology is the application of computer system mathematical control (CNC) systems. CNC systems enable exact control over the stamping process, causing exact and regular production of complex components. Additionally, making use of servo presses has actually brought about improvements in power performance and minimized cycle times, additionally maximizing the production process.
Additionally, the assimilation of automation and robotics has structured metal marking operations by increasing performance and lowering the threat of errors. Automated systems can execute jobs with speed and precision, causing improved overall performance in the assembly line.
Automated Processes for Effectiveness
Use of automated processes in steel marking operations has dramatically boosted performance and productivity in making facilities (Metal Stamping). Automated systems have actually transformed the metal stamping market by streamlining processes, reducing hands-on treatment, and reducing the margin of error. These automated remedies include a variety of technologies, including robot arms, CNC machines, and computerized control systems, that work cohesively to execute complex marking tasks with precision and rate
One key advantage of automated procedures in steel marking is the constant top quality they deliver. By eliminating human error and variants in production, automated systems make sure that each stamped component meets precise specs with marginal issues. Automation makes it possible for continual procedure, significantly reducing downtime for device adjustments and upkeep, thereby making the most of general efficiency.
Furthermore, automated procedures improve security in metal stamping operations by lessening the requirement for manual handling of hefty products and sharp devices. This not only safeguards workers yet also adds to an extra structured and effective process. Finally, the combination of automated more helpful hints processes in steel marking procedures is essential for achieving optimal performance, top quality, and security requirements in contemporary manufacturing environments.
Quality Assurance Procedures in Stamping
Offered the focus on constant top quality and efficiency achieved through automated processes in metal stamping operations, executing durable quality control measures becomes necessary to ensure and promote standards accuracy in stamped components. Quality control in metal marking entails a multi-faceted technique Read Full Article to ensure the integrity and precision of the last items. By integrating these procedures into metal marking procedures, manufacturers can regularly produce premium stamped parts that meet the stringent needs of modern markets.
Enhancing Accuracy Through Innovation
To achieve unparalleled accuracy in metal marking procedures, pioneering innovations are continually being created and integrated right into the manufacturing workflow. Advanced technologies such as laser reducing systems and computer numerical control (CNC) equipments have actually transformed the method metal parts are stamped with utmost precision. By using laser cutting modern technology, producers can achieve complicated and intricate designs with micron-level accuracy, guaranteeing that each stamped part fulfills the strictest top quality requirements.
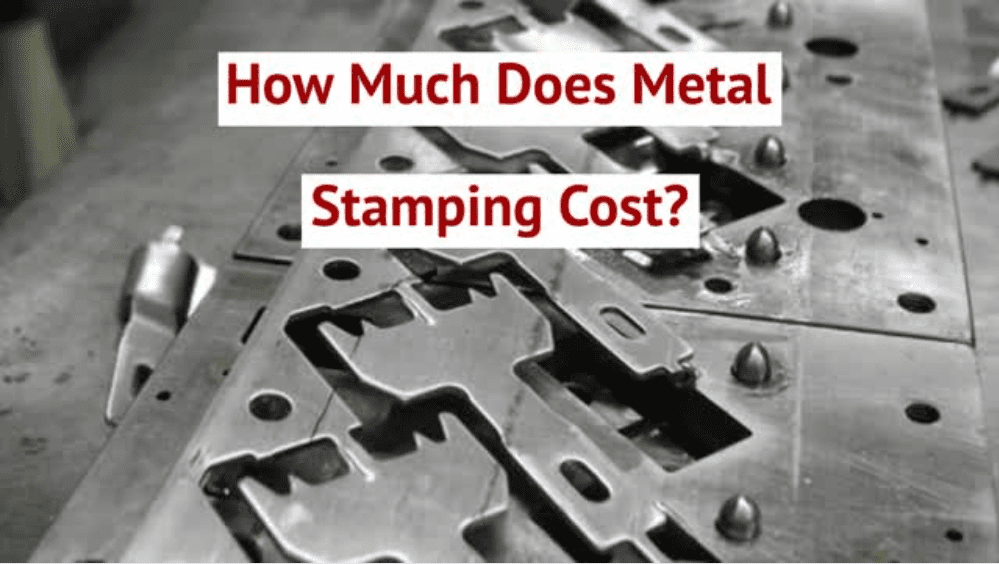
Moreover, using simulation software program allows manufacturers to assess and enhance marking procedures prior to actual production, identifying possible locations for renovation and tweak parameters to achieve optimum accuracy. By accepting these innovative innovations, producers can improve precision, increase efficiency, and supply premium stamped products that satisfy the most stringent needs of modern-day markets.
Carrying Out Lean Manufacturing Practices
Incorporating lean production techniques into metal marking operations can result in streamlined manufacturing processes and increased total performance. By focusing on getting rid of waste, maximizing resources, and continuously boosting processes, steel marking business can enhance efficiency and quality while reducing prices. One essential element of executing lean production in metal marking is the emphasis on developing a effective and smooth operations. This entails organizing workstations, standardizing processes, and lessening unnecessary get redirected here activities to make the most of performance.
Additionally, lean production practices urge a culture of constant enhancement within the organization. By equipping staff members to identify and attend to inefficiencies, business can make step-by-step adjustments that lead to considerable efficiency gains with time. Executing devices such as five, Kanban systems, and worth stream mapping can help enhance procedures, reduce lead times, and improve total high quality in steel marking procedures.
Final Thought
To conclude, the utilization of advanced metal stamping innovations, automated procedures, quality assurance measures, advancement for accuracy enhancement, and application of lean manufacturing practices are essential for making best use of efficiency and top quality in steel stamping procedures. These strategies ensure that items are produced with precision, consistency, and cost-effectiveness. By integrating these sophisticated techniques, makers can stay competitive in the sector and fulfill the needs of clients effectively.
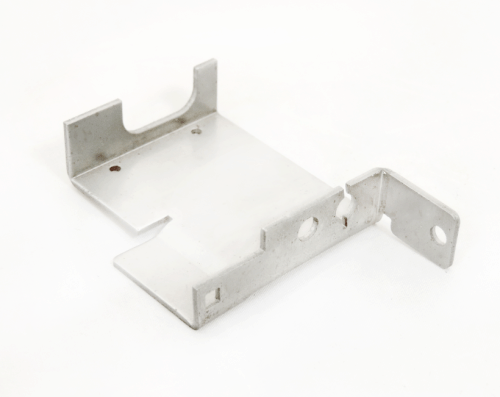
Offered the emphasis on constant high quality and performance attained through automated processes in metal stamping operations, applying robust quality control procedures comes to be essential to guarantee and maintain standards precision in stamped components. Carrying out devices such as Five, Kanban systems, and worth stream mapping can help simplify procedures, reduce lead times, and enhance overall top quality in steel marking procedures.
In verdict, the utilization of sophisticated steel stamping modern technologies, automated procedures, high quality control measures, technology for accuracy enhancement, and application of lean production techniques are essential for maximizing efficiency and top quality in steel stamping operations.
Report this page